Lime - introduction
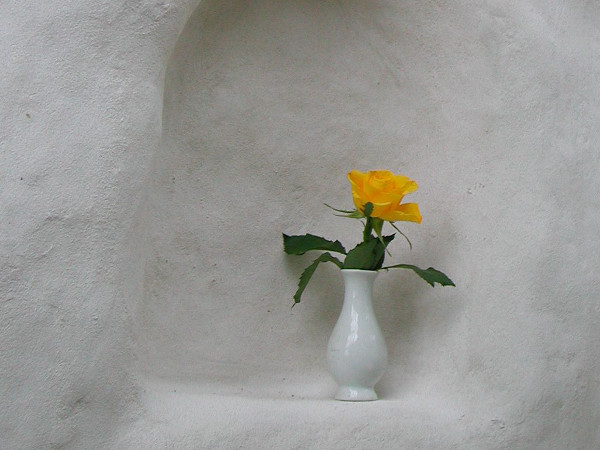
“Ancient structures built using lime, like the Pantheon and the Colosseum, have survived for centuries, often with little to no maintenance.” – Smithsonian Museum
Contents
What is lime?
Lime is a traditional and environmentally-friendly building material that was largely replaced by cement during the 20th Century, but is now coming back into fashion.

Various types of lime are used in building as mortars, renders, plasters, slurries and washes. All are made from limestone, which is a sedimentary rock made from the dead bodies of sea creatures that produce calcium carbonate (coral, shellfish, some planktons). Most limestone was laid down in the Cretaceous period (60-150 million years ago).
Chalk is limestone made from very small white particles.
Slaking quicklime to make lime putty.
The lime cycle
- Limestone is calcium carbonate – CaCO3
- Limestone is burnt in kilns. CO2 is driven off to produce calcium oxide (CaCO3 minus CO2 leaves CaO, or quicklime)
- Quicklime is slaked – i.e. water is added. CaO plus H2O produces Ca(OH)2, or calcium hydroxide (lime putty)
- Lime putty absorbs CO2 from the air to form calcium carbonate (CaCO3) again

Types of lime
Non-hydraulic lime or quicklime is the purest form, made from rocks containing at least 95% calcium carbonate.
Hydrated lime or ‘bag lime’ from builders’ merchants is calcium oxide slaked with a precise amount of water, which is driven off by the heat of the reaction, leaving a powder.
Hydraulic lime is produced from limestone containing clay, and has the added benefit of being able to set underwater.
Here’s more detailed information on the different types of lime.
From the Romans to the mid-18th century, cement was lime plus volcanic ash or other additives. Modern Portland cements and other alternatives to lime date from around WW1.
Fascinating demonstration of the lime cycle. Snail shells (calcium carbonate – CaCO3) are burnt and carbon dioxide is driven off, leaving calcium oxide (CaO, or quicklime). Then water is added to ‘slake’ it, which produces calcium hydroxide, Ca(OH)2. Exposed to the air, it sets, or carbonates, by re-absorbing CO2 from the air – i.e. it becomes calcium carbonate again.
What are the benefits of lime?
Environmental benefits
Carbon neutral: Lime, like cement, gives off CO2 (the main greenhouse gas) during its manufacture. However, it re-absorbs CO2 when it sets, and cement does not.
It is recyclable and biodegradable.
Limestone is burnt at around 900°C compared to around 1300°C for cement. This saves on fuel consumption and emissions of pollution and greenhouse gases.
CO2 emissions in the manufacture of lime are 20% less than for cement.
It is less dense than cement, which saves on transport fuel.

Lime mortars allow bricks to be recycled as you can get the mortar off, unlike cement.
Cements contain heavy metals which are put into the air on burning: lime doesn’t.
It is an important part of any ‘natural house’ – involving timber, straw-bales, lime and earth, all of which are natural, healthy and biodegradable.
Here’s more on the environmental and health benefits of lime.

Benefits for buildings
It is breathable, so any water that enters a structure through a crack, can escape. This isn’t the case with cement.
It is soft and flexible, so if a building moves slightly it won’t crack like cement, and let water in.
With cement mortars, the only way moisture can escape is through the brick, which can begin to erode away.
Here’s more on the benefits of lime for buildings.
What can I do?
It’s interesting to go through whole process, and to slake your own quicklime. It can be dangerous though, as a lot of heat is given off in the reaction. Make sure you understand the health & safety implications.
After slaking your quicklime, and allowing it to cool, you’re left with lime putty, which is the basic constituent of lime mortar, render, plaster and limewash.

Quicklime is a cost-effective way to make lime putty if you slake it yourself – much cheaper than cement.
Mortar: 1 bucket of putty to 4 of sharp sand. The older the mortar the better – it can be kept in airtight bags, and ‘knocked up’ when needed.
Exterior render: 1 part putty to 3 parts sharp sand. Ideally, spray the wall with a weak limewash the day before to provide a key. 2 coats are applied with a trowel or (maybe on a straw-bale wall) by hand (wearing rubber gloves).
How to point a wall using lime mortar.
Interior plaster: first coat 1 part putty, 3 parts sharp sand, plus horse-hair, to bind the plaster. 2nd. coat 1 part putty, 3 parts silver sand (washed and finer), with horse-hair again, cut into 20mm lengths.
Slurry: 1 part putty, 1 part sharp sand. Paint on with a thick paintbrush. Cheap, wonderful texture, will cover anything.

Limewash: 1 part putty, 2 parts water. Can add pigments. Can apply up to 6 coats (one a day) – coats of limewash can be applied very quickly. All lime products need to be applied to a moist surface.
Specialist(s)
The specialist(s) below will respond to queries on this topic. Please comment in the box at the bottom of the page.

Phil Christopher is an environmentalist, builder and trainer and he believes in making a low-impact lifestyle an attractive possibility for everyone. Phil runs Huff and Puff Construction, specialising in straw bale and sustainable building, training and design. He’s a passionate advocate of earthen and lime plasters, stating “It’s the part everyone loves doing, even if they didn’t think they would!”
14 Comments
Hey there! Thank you for all this information. I am now begining the process of building my natural house, and have a few doubts concerning foundations. The plan for foundations is using stones taken from a river that passes near by. Since we are talking about river stones which are rounded, I was thinking it is probably necessary tu use a mortar to put them together. Using regular cement is not an option for us, as the main goal for this house is it being made completely out of natural materials. This is why I was considering using lime morter to put the stones of foundation together… but I do not know about mixes reccomended. Also, I live in an extremely wet area, where humidity in air can raise up to 95% and we have a rainy season that lasts 8 months… so if you have any information about how to use lime in this conditions and for this purpose, I would absolutely appreciate you advice. Thank you so much, and have happy holidays.
Happy New Year Lucía! Broadly speaking, for foundations one would use a natural hydraulic lime, e.g. NHL 5 or NHL 3.5 in a mix with well graded sharp sand. For example, a mix of 1 part NHL 5 to 2.5 parts sand. Or 1 part NHL 3.5 to 1.5 parts sand.
Hopefully you have a good range of stones and sizes. A structural wall’s strength should come from the interlocking of the stones/bricks, not just depend on the mortar. If your river stones leave large gaps between them, use a range of smaller sized stones to fill the voids, in conjunction with your mortar.
You don’t mention what your walls will be made of, however lime is a great external finish on many natural wall types and handles moisture well. However, the biggest initial protection from rain is physical barriers like deep eaves or cladding. I hope this helps!
All the best, Phil.
Thank you again for your response. Super usefull!!
Hi Phil, really interesting article, thank you. We built an earthship with geodesic dome in southern Spain. We covered the dome with padobe then papercrete. After quite a few years and a very heavy downpour Dec ’16 the papercrete on the top of the dome needed another layer, which we did. We also thought a final coating of lime wash would add protection. Where the papercrete was new the lime wash has adhered reasonably well. But where we put it on the older papercrete (even though we wet the surface) it has all but flaked off. We’re not sure what to do now, any advice would be very much appreciated x
Hi Laura,
I can’t take credit for the article, but thank you. I’m afraid I don’t have any experience with papercrete so can’t offer much help. If the papercrete is made using cement than I’m not sure limewash would be able to adhere very well.
I searched and found this article, I don’t know if it will be if any help? And maybe others with more experience will comment. hope you get it sorted. 🙂
All the best,
Phil
Ok, thanks anyway Phil. I’m not seeing a link to the article?
Yes, I’m sorry papercrete is made up with cement, papier-mâché and sand. At the time we didn’t know much about lime render and wanted the insulative properties of papercrete. In hindsight might have been better to use more padobe then lime render. We live and learn!
Many thanks
Laura
Good luck Laura, and this is the link I meant to add: http://www.greenhomebuilding.com/QandA/papercrete/moisture.
All the best,
Phil
Thank you Phil!
Just read the article Phil, yes very useful. Thank you for taking the time to find it for me, much appreciated.
He says he eventually had to cover the papercrete with stucco. I know you said lime wash probably wouldn’t adhere to papercrete because of the cement content, would lime render adhere do you think? We’d really like to keep the breathable aspect that lime offers.
Many thanks again
Laura
Hi Laura,
No worries. 🙂 I’m afraid I really don’t know how porous cement papercrete is, I’ve just assumed it might be low. Presumably incoming water shows it was either porous or cracked? There could still be a number of reasons the lime wash didn’t adhere to the old material. Lack of porosity is one possibility, but it could be how clean and dust free the surface was. I note you said it adhered to the new papercrete well, so perhaps this is a possibility? Also, if the old and new have different porosity, for whatever reason, it’s possible the lime wash took too much or too little time to dry and that affected how it adhered. Equally, the smoothness might be different between the two and that could be it – lime wash needs a decent key. I also don’t know what temperature you have working in (I just assumed it would be a lot warmer than here in the UK!) and obviously any frost would be likely to cause an issue.
It might be worthwhile scrubbing down a small area well, where the lime wash didn’t take, and trying to reapply it, trying a small area with lime wash and making sure it doesn’t dry out too quickly. You could also try an additive of some sort that may help the limewash adhere.
This article covers some of the above and may be of help: http://www.earthpigments.com/limewash/
All the best,
Phil
Gosh, so much to consider! Thank you for giving me a real insight into what may be the problem. And thank you for the link to the article, again great info.
Papercrete is breathable so yes porous. It’s also fairly flexible so not prone to cracking like concrete. But I think we did have a couple of hairline cracks. Also we had only done a first layer always planning to do a second. Only torrential rains got to us first which is when we suffered leaks. The new layer is really smooth so it’s weird that the lime wash is sticking better to that.
We’ll do as you suggest and try a small area of the older crete. Maybe it was too hot when we did it last year too so will allow for that.
Thank you so much, really appreciate your advice
All the best
Laura
To the web site editor:
Over on the “Lime plasters and renders” page the coverage calculation is a bit wonky if I may say so.
Somehow 1 cubic metre of render has been taken to weigh one tonne, which is incorrect. I wouldn’t throw 1 cu.m of render on the back of my 1 tonne flat bed truck (if I had one) unless I wanted to destroy it. It would weigh nearly 3 tonne.
Best to forget weights and stick to volumes. So the calculation just needs to replace “tonne” with “cu.m”.
But then there’s a second more critical error unless I’m mistaken, which is often.
The volume of lime putty required to make 1 cu.m of 3:1 render is not 250 kg nor 250 litres, but 333 litres. This is because the putty is filling the voids in the sand and therefore not adding to the volume of render. To make 1 cu.m of 3:1 render you’ll need 1 cu.m of sand plus 333 litres of lime putty. Now, a 25kg tub of lime putty will fit into about 19 litres (the specific gravity of lime putty is about 1.35), so you’ll need about 19 tubs, not 10.
As in the example, that 1 cu.m of render will cover 100 sq.m of wall to a depth of 1cm, or 50 sq.m with two coats.
Hi Rocso, Thank you for your excellent comment and I’m very sorry it’s taken so long to get back to you. I’m not sure who wrote the original article, but we are checking through the details and will soon update the measurements accordingly. Thank you! 🙂
We are calcined lime powder manufacturers in india of Calcined Lime, Hydrated Lime, Dolomite Lime and Limestone. We have our manufacturing facility in multiple locations. Initially the group was introduced to Lime manufacturing in 1984 through supply of steam coal to Lime Kilns. Demand for Lime was huge in western part of India mainly due to number of Sugar factories and our group picked upon the opportunity.