Weaving - introduction
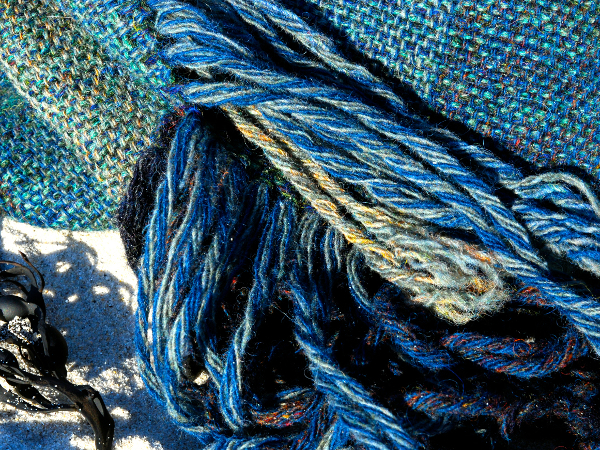
pic: These Isles
“To care about weaving, to make weavings, is to be in touch with a long human tradition. We people have woven, first baskets and then cloth, for at least ten thousand years.” – Phylis Morrison
Contents
What is weaving?
There are four fundamental ways of making a textile: felting, knitting, knotting or weaving. Weaving is among the most widespread: whereas knitted fabric is best for stretchy clothing, a woven cloth is structurally more stable (and won’t unravel in quite the same way), and similarly scaleable with mechanisation. The basic principle is that a grid of threads criss cross under and over each other. Spun fibre is usually used, woven on a simple or complex mechanical or electronic machine called a loom.

Most domestic looms consist of some sort of wooden frame and a means of interlacing longitudinal and latitudinal threads. Industrial looms are usually steel. Complex fabric design patterns are now largely computer generated for the mass market. However, ‘primitive’ technology can still be used at home for a variety of uses. Depending on the resources, equipment, time and patience you have, you can make a range of clothing and household items: shawls, scarves, snugs, snoods, cowls, ponchos, cushions, bags, rugs, mats, coasters, upholstery, curtains, blinds, hangings, tapestries, blankets, towels, tea towels, dish cloths, and, on larger looms, cloth that can be used for tailored clothing, shoemaking and almost any other purpose according to its properties. Many industrial items are or used to be woven too: vehicle upholstery; gas masks; waxed linen fire hoses and other water containers etc.
Every traditional culture has or had its own style and method of weaving, using differently fashioned looms and tools. There’s evidence of weaving going back to the Stone Age, but it’s very unusual to find ancient pieces preserved because textiles made from natural fibres are biodegradable. However, a 4-8,000 year old nettle textile was uncovered in 2016 on Whitehorse Hill in the acid peat soil of a Neolithic burial tomb.
Adding texture on a rigid heddle loom. From our weaving online course.
The basic weaving process
Weaving is a way of making cloth/textiles using spun fibre on some sort of loom (although sometimes unspun fibres can be used – on a peg loom, for example). The vertical threads are called the warp, and the horizontal threads that are woven through them are called the weft. The warp is made on the loom, and tied to it in different ways, depending on the type of loom. The warp is tensioned and threaded through a ‘heddle’. A space (or a ‘shed’) has to be made in the warp to allow the weft through. This is done by raising or lowering the heddle, then the weft is threaded through the shed, either by hand or via a shuttle or bobbin loaded with yarn. Then the next shed is opened, and the weft passed back through for the next layer. This process is repeated until the fabric is the size you require, after which you cut and tie the warp, and you have your finished piece, which can then be set by moistening and pressing so that the stitches stay in place for a well-structured fabric.
Types of loom
In rough order of complexity starting with the simplest, here are some kinds of looms that can be readily used, or even made, at home:

Peg loom: especially good for very chunky fabrics (think oversize knitting) like mats, a peg loom is simply a row of wooden pegs protruding from a wooden base that helps them stand upright on a flat surface. It can be made by drilling 9mm holes into a board, at least 9mm apart depending on yarn thickness, and inserting 15cm long pegs with a hole drilled through each at the base as it protrudes from the board. The strong warp threads, of any thickness, are passed through the holes in the pegs. Then the weft is woven around each peg in the row until they are full to the top. The pegs are then removed and the woven weft pulled down onto the free warp (which can be knotted or weighted if tautness makes the weaving easier). The pegs are then replaced in their holes and the process is repeated, increasing the size of the weaving each time. Peg looms can be used to make peg loom rugs, seat mats or bags with unspun fleece, so making and processing time is reduced.

Backstrap loom: used in South America and the Far East, these are the width of a human. The ends of the warp are tied to a post or a tree, and a strap goes round your back. As you lean back, it tensions the warp, while flat sticks turned on their sides lift alternate sets of ends in turn while the weft is passed through the shed with a bobbin. Colourful patterned textiles are made this way, most famously in Guatemala and Peru.

Navajo loom: a native American frame that is usually simple, robust, large and upright, and most iconically used for rugs, blankets and saddle blankets.

Inkle loom: small, narrow and very portable, drawing on the ingenious card system for making patterned belts, straps and other ornate and functional ribbons of fabric.
The following looms, if weaving fabric wider than 20cm or so, will require some sort of shuttle as a vehicle for passing the weft through the shed.

Brinkley loom: a very simple wooden frame used in a horizontal position but which can rotate around a central axis (a broom stick!) for winding the warp (longitudinal threads) in situ. Speedy and easy as the loom is dressed in minutes at the same time as the warp is wound. See here for a demo.

Rigid heddle loom: a good, introductory all-rounder, the rigid heddle loom is a simple frame, often used on a table. It’s versatile and can be used to produce almost anything, including fine or chunkier fabric and they’re available in lots of widths – up to 1.2m wide. They can create fabric for clothing, tea towels or be used to make tapestries or wall hangings. The rigid heddle is used in a different way to the ‘shafts’ on a table or floor loom. The holes and slots enable a ‘shed’ or gap to be created, through which the shuttle passes, but patterns are produced in a different way. Heddles come in several different sizes for versatile weaving. A second heddle can be added and the two are used together in order to weave fabric with a warp as fine as 25 threads to the inch (10 per cm).

Tapestry loom: a simple, upright frame used for slow, meticulous patterns and especially image-making as many coloured wefts, bundled into small butterfly knots for easy unwinding in action, can be woven through small sections of the warp to build up pictures from bottom to top. The weft is packed down hard with a tapestry beater (large wooden fork) so that it entirely covers the warp.
Making a raw wool rug on a hand loom.
Rugmaking loom: normally upright or horizontal floor looms with two foot operated shafts, rather than being simple frame looms. They have to be very strong as rugs are often beaten down firmly using a weighted beater.

pic: These Isles
Table loom: compact loom which is nonetheless sometimes wide enough to weave a blanket or expanse of cloth (if you’re time-rich, patient and skilled). At 56cm or sometimes even 82cm wide, it is very versatile. The weaving width can be doubled or you can make tubes (useful for bags and cushions) simply by changing the shaft lifting pattern. A table loom can take either a thick warp which is quicker to work and makes a chunkier fabric from upwards of about 5 ends per inch (or 2 per cm), or a fine warp with even one or two thousand ends passing through 500 heddles or more. It sits on a table, is best operated standing up, and the ‘castle’ or central elevated frame holds between four and 16 shafts. The greater the number of shafts, the more complex the patterns allowed.

Floor/treadle loom: a larger, freestanding loom operated sitting down and enabling larger and faster weaving by virtue of pedals (‘treadles’ usually made from wood and attached to the shafts with strings that lever over the castle). It employs the same number of treadles as shafts to change the shed with your feet – i.e. to lift alternate threads depending on the number of shafts and the kind of pattern you want. This frees up your hands to attend only to the weft.
Weave patterns
There are different kinds of weaves according to both the patterns sought and the fabric properties required (strength, durability, softness, stretch etc.).
In a plain weave the weft goes over and under each warp thread (and a balanced plain weave has warp and weft threads of the same thickness, making a simple square pattern). An ordinary cotton shirt will often be made in plain weave.
In a twill weave the weft covers two out of four warp threads to make a thicker, stronger fabric – denim is a twill.

In a satin weave, the weft passes over even more warp threads to produce a very smooth fabric.
If the weft completely covers the warp in a sturdy ‘weft-faced’ fabric, it’s called a tapestry weave.
Plainer weaves can accentuate the character of the yarns, are faster to make, and free up the weaver from intense concentration to experiment with texture and colour. Patterned fabrics, requiring greater patience, time and skill, can be made using more complex weave patterns on looms with four or more shafts.

What are the benefits of weaving?
Methodical, systematic and design-oriented, weaving is simultaneously soothing and technically challenging for creatives and engineers alike. A lot of 20th century occupational therapy was shaped around weaving as therapy. Clothmaking for traumatised WW1 veterans followed on from the basketry taught to sufferers of mental health conditions in asylums before that. Occupational therapist Shoshanah Shear remarks on benefits ‘in improving upper limb function, hand function, concentration, patience, work speed, work tolerance, standing tolerance’, to which can be added hand-eye co-ordination, dexterity, and, significantly, reduction of anxiety.
Practising weaving enables low-impact production of unique items for the household, as gifts or for sale. Cottage industry offers a sustainable alternative to corporate mass production or wage slavery. (You can slave for a pittance for yourself, instead!).

What can I do?
First, learn as much as you can. Here’s our free online course on all aspects of weaving. The tutor is Janet Renouf-Miller of Create With Fibre.
You may also have a friendly local Guild of Weavers, Spinners and Dyers group that you can join; and/or simply teach yourself.
First consider what you want to weave, and then choose a loom – or consider what you can weave with whichever loom you can make or acquire.
More sustainable fibres (depending on your location, how they’re produced, on what scale, and on how far they’ve travelled) include nettle (for ramie), flax (for linen), hemp, wool, organic cotton, banana silk, and bamboo (for rayon).

Source wool from small, trusted, nearby (rare) breeders, to avoid ‘sheepwrecking’, and source plant fibres from organic and small growers. To reduce fossil fuel dependency, resist the power of the oil industry, and lower your carbon footprint, avoid petro-fibres. These are polymer-based synthetics like the all-too-common acrylic, nylon and polyester – plastics, in other words. (Recycled petro-fibre clothes reduce plastic bottles etc. to microbeads, which are an even greater envionrmental hazard.) Make a non-toxic, breathable and biodegradable fabric instead.
Choose a warp that is strong and even, with a high enough twist for strength but not so twisty that the wool springs into curls when relaxed off the cone or ball. Handspun yarn is generally harder to work with as a warp if it’s irregularly spun, which it often will be. However, you can make your own yarn for weaving by carding your own fleeces (or even shearing your own sheep); or by growing and processing natural fibres, then spinning and vegetable dyeing them yourself too.

Eventually, a scarf can be made in a day, and a blanket in three or four days, depending on your process. If you account for your time, items will appear expensive – most low-impact methods cost less in resources and more in labour. (The converse is also true: mechanisation and economies of scale tend to come at a higher environmental, as well as socio-economic, price).
Q: Why weave your own clothes, grow your own veg or make your own furniture, when you could work more in paid employment, and buy those things from a supermarket or a sweatshop?
A: For pleasure, fulfilment, resilience, autonomy, therapy, skillbuilding and skill conservation; for the local economy; and especially for the lower environmental impact of producing useful items sustainably, right here at home, just as you want and need them.
Free online course
Here’s our free online course on all aspects of weaving. The tutor is Janet Renouf-Miller of Create With Fibre.
Specialist(s)
Thanks to Eloise Sentito of These Isles, Janet Renouf-Miller of Create with Fibre and Jane Meredith of Plant Dyed Wool for information, and Eloise for main image.
The specialist(s) below will respond to queries on this topic. Please comment in the box at the bottom of the page.

Janet Renouf-Miller runs Create with Fibre, and is a registered teacher with the Association of Weavers Spinners and Dyers and has taught at their renowned Summer School. Janet has also taught courses for many spinning and weaving Guilds, knitting groups, shops and voluntary organisations. She is the author of How to Spin (just about anything) and tutor of our weaving online course.
2 Comments
I already have a 32 inch rigid heddle loom but I’m thinking of giving up the width for the warping speed of a brinkley loom but can I only do tabby weave on it? No way to double heddle but can I use pick up?
Hi Kate
Most people do find the Brinkley faster to warp. However I would seriously consider a smaller rigid heddle loom, which will be more versatile and continue to be useful as your weaving skills develop. People often buy a wide loom thinking it will be more versatile but then find out that the opposite is the case and of course the less warp threads there are the faster it is to warp. Think about using a heddle with wider spacing too. Eg a 5 dent for Aran weight yarn and a 7.5 dent for Double knitting weight yarn. Look out for the forthcoming Low Impact e-course on weaving, which will cover all of this and show you how to warp the rigid heddle loom easily and quickly.